Die Welt der Metallbearbeitung steht heute vor einer wichtigen Weichenstellung: Faserlaser haben in den letzten Jahren den Markt revolutioniert, während bewährte Technologien wie Plasma- und Brennschneidanlagen weiterhin ihre Berechtigung behalten. Für Unternehmen stellt sich dabei die zentrale Frage: Welche Technologie ist die richtige Investition?
Die Entscheidung für eine bestimmte Schneidtechnologie beeinflusst nicht nur die Qualität Ihrer Produkte, sondern auch Ihre Produktionseffizienz und Betriebskosten. Jedes Verfahren – ob modernster Faserlaser, vielseitige Plasmaschneidanlage oder robuste Brennschneidanlage – bringt seine eigenen Vor- und Nachteile mit sich.
In diesem Artikel analysieren wir die drei führenden Technologien im Detail und geben Ihnen konkrete Entscheidungshilfen an die Hand. Wir betrachten dabei nicht nur technische Aspekte, sondern auch wirtschaftliche Faktoren wie Anschaffungskosten, Betriebskosten und Produktivität. Unser Ziel ist es, Ihnen eine fundierte Grundlage für Ihre Investitionsentscheidung zu bieten.
Faserlaser: Die moderne Präzisionslösung
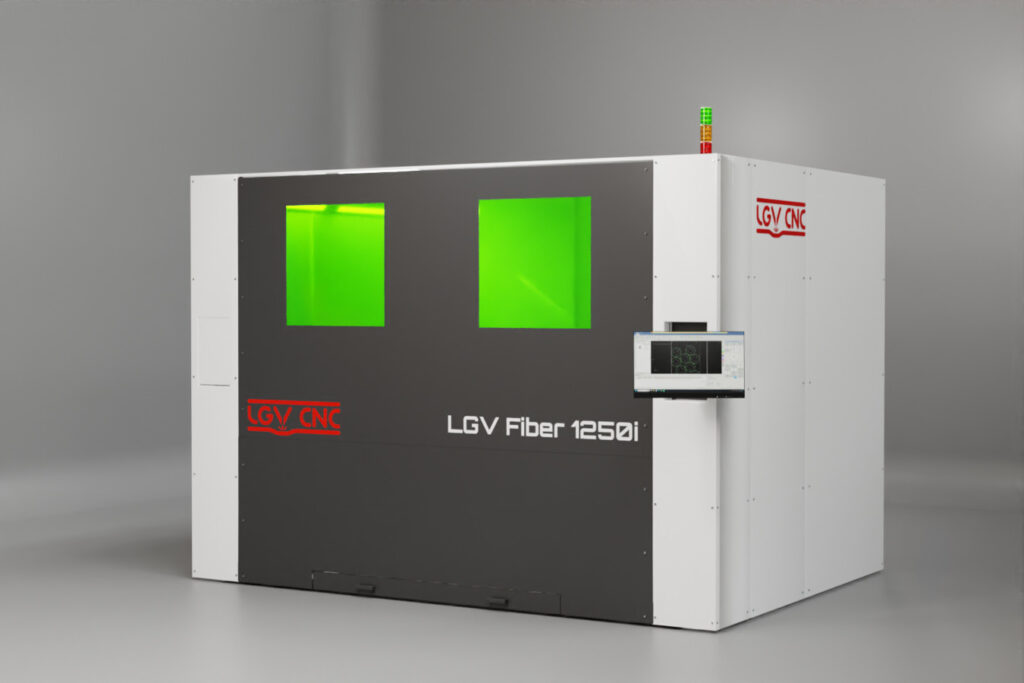
Die Einführung des Faserlasers hat die Metallbearbeitung grundlegend verändert. Diese innovative Technologie setzt neue Maßstäbe in Sachen Präzision und Effizienz, wodurch sie sich deutlich von konventionellen Schneidverfahren abhebt. Besonders bei der Bearbeitung von Metallblechen zeigt der Faserlaser seine beeindruckenden Stärken.
Das Herzstück der Technologie bildet ein hochkonzentrierter Laserstrahl, der durch eine flexible Glasfaser zum Schneidkopf geführt wird. Diese intelligente Konstruktion ermöglicht nicht nur äußerst präzise Schnitte mit minimaler Wärmeeinflusszone, sondern erreicht auch beachtliche Schnittgeschwindigkeiten von bis zu 40 Metern pro Minute bei dünnen Blechen. Die schmale Schnittfuge von unter 0,1 Millimetern unterstreicht dabei die außergewöhnliche Präzision dieser Technologie.
In der Praxis überzeugt der Faserlaser besonders bei der Bearbeitung von dünnen bis mittleren Blechstärken zwischen 0,5 und 25 Millimetern. Selbst hochreflektierende Materialien wie Kupfer oder Messing, die für andere Schneidverfahren eine echte Herausforderung darstellen, lassen sich problemlos bearbeiten. Die Technologie brilliert vor allem dort, wo filigrane Konturen und komplexe Geometrien gefragt sind – ein entscheidender Vorteil in der modernen Fertigung.
Wirtschaftlich betrachtet erfordert die Anschaffung einer Faserlaser-Schneidanlage zwar eine höhere Anfangsinvestition, dies wird jedoch durch die deutlich niedrigeren Betriebskosten über die Zeit ausgeglichen. Der geringe Energieverbrauch und minimale Wartungsaufwand tragen zur ausgezeichneten Gesamteffizienz bei. Hinzu kommt die hohe Produktivität durch schnelle Bearbeitungszeiten und kurze Rüstphasen.
Dennoch gibt es auch Grenzen: Bei sehr dicken Materialien stoßen Faserlaser an ihre wirtschaftlichen Grenzen. Zudem erfordert der Betrieb geschultes Personal und die Einhaltung spezieller Sicherheitsvorschriften. Diese Faktoren sollten bei der Investitionsentscheidung sorgfältig abgewogen werden.
Plasmaschneiden: Der vielseitige Allrounder
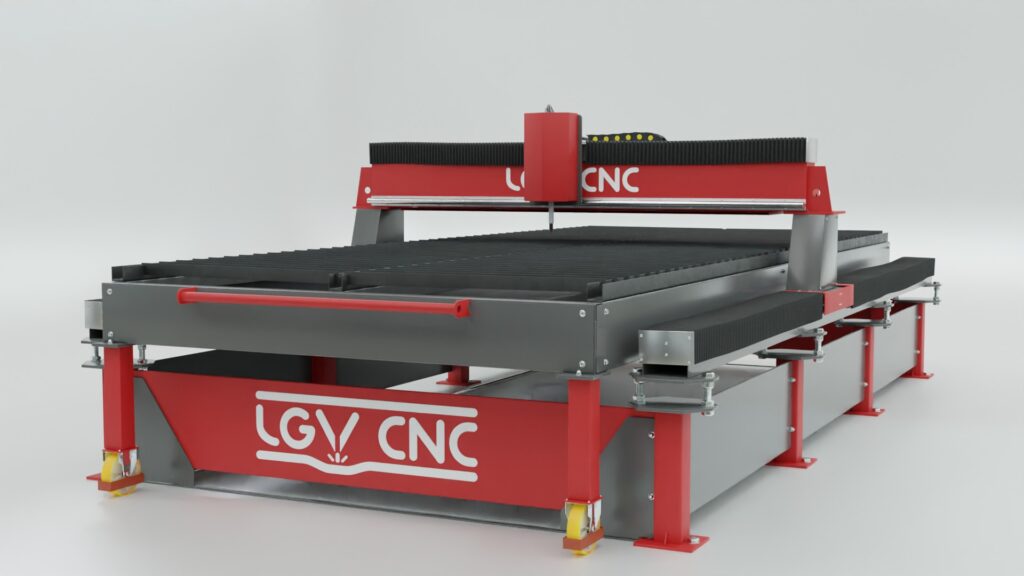
Die Plasmaschneidanlage hat sich als zuverlässige Lösung in der Metallbearbeitung etabliert. Mit über 30 Jahren Markterfahrung und kontinuierlicher technologischer Weiterentwicklung überzeugt das Verfahren durch sein ausgewogenes Verhältnis von Kosten und Leistung. Aktuelle Marktdaten zeigen, dass etwa 45% aller metallverarbeitenden Betriebe in Deutschland Plasmaschneidsysteme einsetzen.
Die Technologie nutzt einen elektrisch leitfähigen, hochenergetischen Plasmastrahl, der Temperaturen von bis zu 30.000°C erreicht. Diese extreme Hitze ermöglicht Schnittgeschwindigkeiten von 6 Metern pro Minute bei 20mm Materialstärke – deutlich schneller als beim konventionellen Brennschneiden. Moderne High-Definition-Plasmasysteme erreichen dabei eine Schnittqualität, die in vielen Anwendungsfällen mit dem Faserlaser konkurrieren kann.
Besonders wirtschaftlich zeigt sich die Plasmaschneidanlage im mittleren Dickenbreich:
- Optimaler Arbeitsbereich: 3 bis 38mm Materialstärke
- Maximale Schneiddicke bei Baustahl: bis zu 75mm
- Energieeffizienz: etwa 60% günstiger im Betrieb als Faserlaser bei Materialstärken über 20mm
- Investitionskosten: durchschnittlich 40-50% niedriger als bei vergleichbaren Faserlaseranlagen
Ein weiterer bedeutender Vorteil ist die Materialvielfalt. Aktuelle Systeme schneiden problemlos:
- Konstruktionsstahl (bis 75mm)
- Edelstahl (bis 50mm)
- Aluminium (bis 40mm)
- Kupfer und Messing (bis 30mm)
Die Betriebskosten fallen moderat aus. Eine Analyse von 100 mittelständischen Betrieben zeigt durchschnittliche jährliche Wartungskosten von 3.000 bis 5.000 Euro. Die Verbrauchskosten pro Schneidmeter liegen je nach Material zwischen 0,15 und 0,40 Euro – ein überzeugendes Argument für kostenorientierte Unternehmen.
Allerdings gibt es auch Einschränkungen: Die Schnittqualität erreicht nicht ganz das Niveau eines Faserlasers, und die Wärmeeinflusszone ist mit 0,2 bis 0,5mm etwas größer. Bei sehr dünnen Blechen unter 1mm arbeitet das System weniger präzise. Dennoch bietet die Plasmaschneidanlage für viele Anwendungen das beste Preis-Leistungs-Verhältnis am Markt.
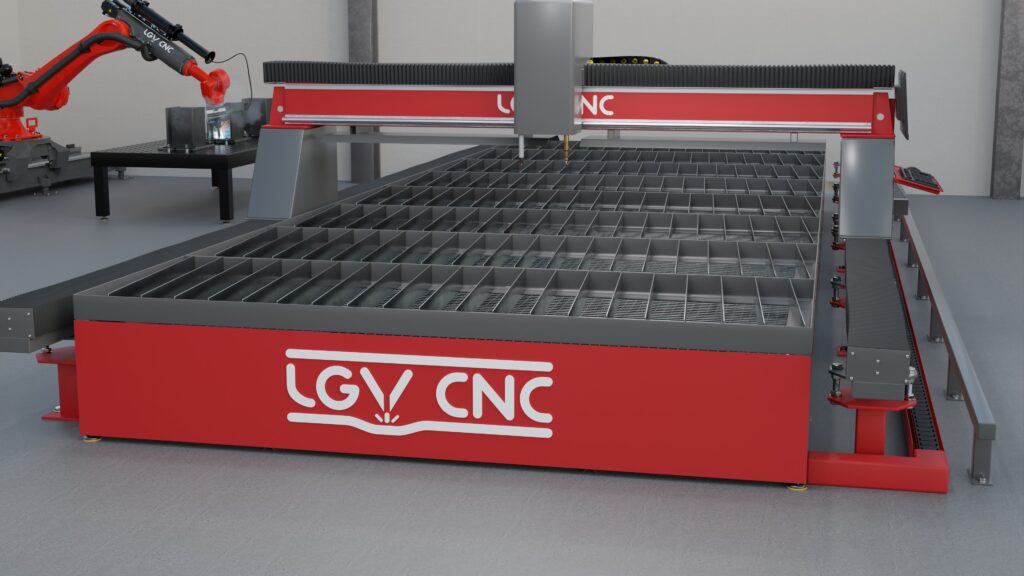
Das autogene Brennschneiden, auch unter dem Begriff Brennschneidanlage bekannt, verkörpert das fundamentale Prinzip der thermischen Trennung von Metallen. Diese Technologie, die seit über 100 Jahren kontinuierlich weiterentwickelt wurde, behauptet sich auch heute noch als unverzichtbares Verfahren – besonders wenn es um die Bearbeitung dicker Materialien geht.Im Kern basiert die Technologie auf einer exothermen Reaktion: Ein Gemisch aus Brenngas und Sauerstoff erhitzt das Material auf Zündtemperatur (etwa 1.300°C), woraufhin ein konzentrierter Sauerstoffstrahl den eigentlichen Schneidprozess einleitet. Diese simple aber effektive Methode bringt entscheidende Vorteile mit sich:
Stärken im Dickblechbereich
- Materialstärken von 3mm bis zu beeindruckenden 300mm möglich
- Keine Obergrenze bei der Schnitttiefe (mehrlagiges Schneiden möglich)
- Gleichbleibend gute Schnittqualität auch bei extremen Materialstärken
- Ideal für Stahlbau und Schwerindustrie
Wirtschaftliche Aspekte
- Niedrigste Investitionskosten der drei VerfahrenGeringe Betriebskosten durch einfache Verbrauchsmittel
- Robust und langlebig mit minimalen Wartungsanforderungen
- Keine speziellen Schulungen für Bedienpersonal erforderlich
Allerdings bringt die Technologie auch charakteristische Einschränkungen mit sich:
- Relativ langsame Schnittgeschwindigkeit im Vergleich zu Plasma und Laser
- Ausschließlich für unlegierten Stahl geeignet
- Größere Wärmeeinflusszone als bei anderen Verfahren
- Weniger präzise bei komplexen Konturen
Moderne Brennschneidanlagen kombinieren dabei häufig traditionelle Stärken mit zeitgemäßer Steuerungstechnik. CNC-gesteuerte Systeme ermöglichen heute eine Präzision, die für viele industrielle Anwendungen völlig ausreichend ist. Die Technologie bleibt damit besonders für Unternehmen attraktiv, die regelmäßig dicke Stahlbleche bearbeiten müssen.Ein weiterer Pluspunkt ist die Möglichkeit der Kombination: Viele Hersteller bieten heute Mehrkopf-Systeme an, die gleichzeitig mehrere Teile schneiden können. Dies kompensiert die geringere Schnittgeschwindigkeit und macht die Brennschneidanlage gerade bei der Serienfertigung dicker Bauteile hocheffizient.
Fazit: Die richtige Schneidtechnologie für Ihren Erfolg
Die Wahl der optimalen Schneidtechnologie hängt maßgeblich von Ihren spezifischen Anforderungen ab. Während der Faserlaser in der Präzisionsfertigung und bei dünnen bis mittleren Materialstärken brilliert, überzeugt die Plasmaschneidanlage durch ihr ausgewogenes Preis-Leistungs-Verhältnis. Das Brennschneiden behält seinen festen Platz in der Dickblechbearbeitung.
Unsere Analyse zeigt:
- Faserlaser: Ideal für präzise Teile und hohe Stückzahlen
- Plasma: Der Allrounder für vielseitige Anforderungen
- Brennschneiden: Der Spezialist für dicke Materialien
Ihr Weg zur optimalen Lösung
Die LVG CNC ist Ihr kompetenter Partner für alle drei Schneidtechnologien. Mit jahrelanger Erfahrung in der Metallbearbeitung berät Sie das Expertenteam der LVG CNC individuell und herstellerunabhängig. Sie profitieren von:
- Ausführlicher technischer Beratung
- Wirtschaftlichkeitsberechnungen für Ihren spezifischen Fall
- Testschnitten auf Wunsch
- Umfassendem Service nach dem Kauf
Vereinbaren Sie jetzt ein persönliches Beratungsgespräch mit den Experten der LGV CNC. Kontaktieren Sie uns für eine fundierte Analyse Ihrer Anforderungen und eine maßgeschneiderte Empfehlung.
Investieren Sie in Ihre Zukunft – mit der richtigen Technologie für Ihre Anforderungen.
Schreibe einen Kommentar