Inhaltsübersicht:
- 1. Wirkungsgrade verschiedener Schneidtechnologien.
- 2. Geschwindigkeitsfaktor: Effizienz pro Produktionseinheit
- 3. Nebenaggregate und versteckte Energieverbraucher
- 4. Wirtschaftliche Dimension der Energieeffizienz
- 5. Ökologische Vorteile durch verbesserte Energieeffizienz
- 6. Effizienzoptimierung durch intelligente Steuerung
- 7. Materialeffizienz als zusätzlicher Umweltfaktor
- 8. Fazit: Faserlaser als Effizienzgewinner
In Zeiten steigender Energiepreise und wachsenden Umweltbewusstseins rückt die Energieeffizienz von Fertigungstechnologien zunehmend in den Fokus.
Besonders bei der Metallbearbeitung, einem energieintensiven Prozess, können effizientere Technologien erhebliche wirtschaftliche und ökologische Vorteile bieten. Dieser Beitrag vergleicht Faserlasertechnologie mit herkömmlichen Schneidverfahren und beleuchtet die Effizienzpotenziale.
Wirkungsgrade verschiedener Schneidtechnologien
Die Effizienz einer Schneidtechnologie lässt sich am Wirkungsgrad messen – dem Verhältnis zwischen eingesetzter Energie und tatsächlich für den Schneidprozess genutzter Energie:
- Faserlaser: 30-40% Wirkungsgrad
- CO₂-Laser: 10-15% Wirkungsgrad
- Plasmaschneiden: 7-12% Wirkungsgrad
- Autogenes Brennschneiden: 5-8% Wirkungsgrad
Diese Unterschiede wirken sich direkt auf den Stromverbrauch aus. Ein 4kW-Faserlaser benötigt typischerweise eine elektrische Anschlussleistung von 15-18 kW, während ein vergleichbarer CO₂-Laser 25-30 kW und ein Plasmaschneider mittlerer Leistungsklasse 30-40 kW verbraucht.
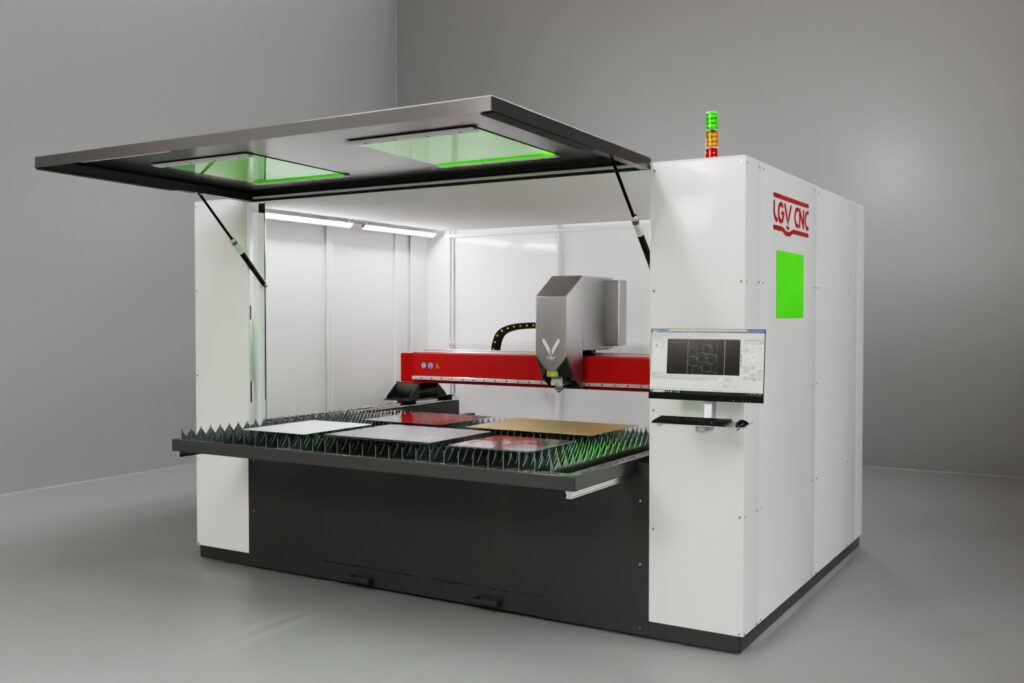
Geschwindigkeitsfaktor: Effizienz pro Produktionseinheit
Der reine Wirkungsgrad allein erzählt jedoch nur die halbe Geschichte. Entscheidend für die Energieeffizienz ist der Energieverbrauch pro produziertem Teil. Hier spielt die Schnittgeschwindigkeit eine zentrale Rolle:
Material | Faserlaser | CO₂-Laser | Plasma | Autogen |
1mm Edelstahl | 25 m/min | 10 m/min | 8 m/min | nicht möglich |
3mm Edelstahl | 8 m/min | 3,5 m/min | 3 m/min | nicht möglich |
6mm Baustahl | 3,5 m/min | 2 m/min | 2,2 m/min | 0,5 m/min |
15mm Baustahl | 1,2 m/min | 0,8 m/min | 1,5 m/min | 0,4 m/min |
Diese Geschwindigkeitsvorteile, besonders bei dünnen bis mittleren Materialstärken, führen zu einer überproportionalen Effizienzsteigerung:
Fallbeispiel: Bei der Produktion von 1.000 identischen Bauteilen aus 3mm Edelstahl ergibt sich folgende Energiebilanz:
- Plasmaschneider: 40 kW × 40 Stunden = 1.600 kWh
- CO₂-Laser: 30 kW × 34 Stunden = 1.020 kWh
- Faserlaser: 18 kW × 15 Stunden = 270 kWh
Der Faserlaser verbraucht in diesem Beispiel nur 17% der Energie des Plasmaschneiders und 26% der Energie des CO₂-Lasers.
Zum Schnittkostenrechner
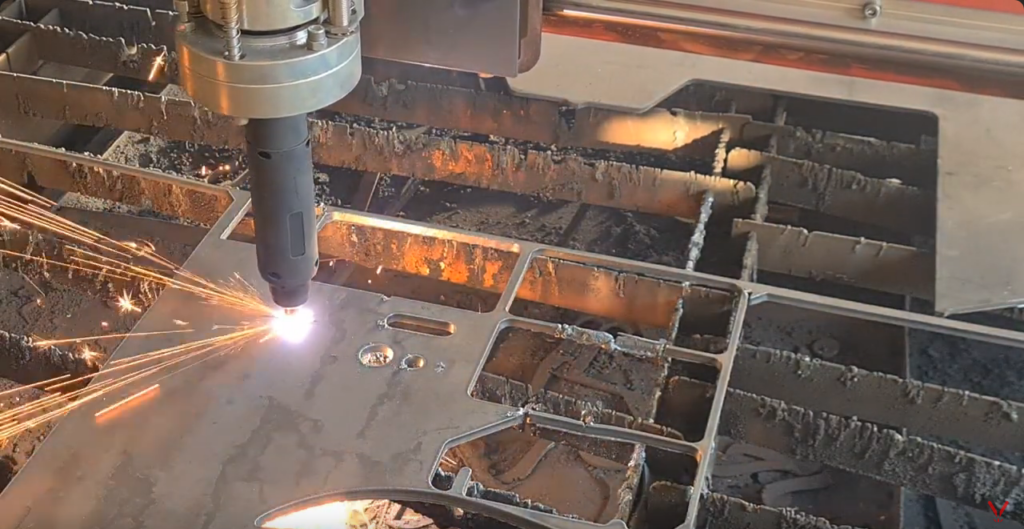
Nebenaggregate und versteckte Energieverbraucher
Bei einer ganzheitlichen Betrachtung müssen auch die Nebenaggregate berücksichtigt werden:
Plasmaschneiden:
- Drucklufterzeugung: 5-10 kW zusätzlicher Energiebedarf
- Wasserkühlsysteme: 2-4 kW
- Filteranlagen für erhöhte Rauchentwicklung: 3-7 kW
CO₂-Laser:
- Komplexe Gaskühlung: 4-8 kW
- Gasversorgung (Helium, CO₂): Energieaufwand für Produktion und Transport
- Vakuumpumpen: 2-3 kW
Faserlaser:
- Einfachere Luftkühlung: 2-3 kW
- Geringerer Filterbedarf durch saubereren Schnitt: 2-4 kW
Diese zusätzlichen Verbraucher können die Gesamtenergiebilanz nochmals deutlich beeinflussen und den Vorteil der Faserlasertechnologie verstärken.
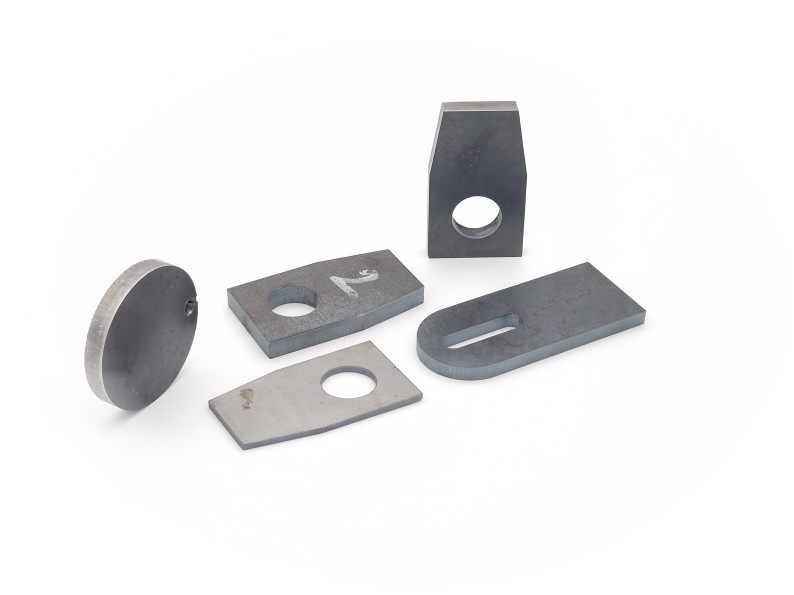
Wirtschaftliche Dimension der Energieeffizienz
Der Energieverbrauch schlägt sich direkt in den Betriebskosten nieder. Bei einem industriellen Strompreis von 0,20 €/kWh und 2.000 Betriebsstunden jährlich ergeben sich folgende Einsparungen:
- Umstieg von Plasma auf Faserlaser: ca. 11.000-12.000 €/Jahr
- Umstieg von CO₂-Laser auf Faserlaser: ca. 5.000-6.000 €/Jahr
Bei einer typischen Nutzungsdauer von 10 Jahren bedeutet dies Einsparungen von 50.000-120.000 € allein bei den Energiekosten
Zum Schnittkostenrechner
Ökologische Vorteile durch verbesserte Energieeffizienz
Die Energieeinsparung wirkt sich direkt auf den CO₂-Fußabdruck aus. Basierend auf dem durchschnittlichen EU-Strommix (ca. 275g CO₂/kWh) ergeben sich folgende jährliche Einsparungen:
- Umstieg von Plasma auf Faserlaser: ca. 18-20 Tonnen CO₂
- Umstieg von CO₂-Laser auf Faserlaser: ca. 8-10 Tonnen CO₂
Für Unternehmen, die jährlich 500 Tonnen Metall verarbeiten, bedeutet der Einsatz eines Faserlasers im Vergleich zum Plasmaschneiden eine Reduzierung der CO₂-Emissionen um etwa 25-30%, was einem durchschnittlichen PKW-Jahresausstoß von 30-40 Fahrzeugen entspricht.
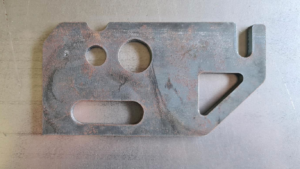
Effizienzoptimierung durch intelligente Steuerung
Moderne Faserlaseranlagen bieten zusätzliche Effizienzpotenziale durch intelligente Steuerungssysteme:
- Bedarfsgerechte Leistungsregulierung: Automatische Anpassung der Laserleistung an Materialstärke und -typ
- Stand-by-Management: Reduzierung des Energieverbrauchs in Produktionspausen um bis zu 90%
- Resonatoroptimierung: Kontinuierliche Anpassung der Laserparameter für optimalen Wirkungsgrad
Diese Systeme können den Energieverbrauch nochmals um 10-15% senken.
Materialeffizienz als zusätzlicher Umweltfaktor
Die höhere Präzision von Faserlasern wirkt sich auch auf die Materialeffizienz aus:
- Schmalere Schnittfugen (0,1-0,2 mm vs. 1-2 mm bei Plasma)
- Geringerer Materialverzug ermöglicht engeres Nesting
- Reduzierter Ausschuss durch höhere Schnittqualität
Dadurch können 3-7% des Rohmaterials eingespart werden, was bei einem jährlichen Materialverbrauch von 100 Tonnen und einem Preis von 3.000 €/Tonne Einsparungen von 9.000-21.000 € bedeutet – und gleichzeitig die in der Materialherstellung gebundene Energie (Graue Energie) reduziert.
Fazit: Faserlaser als Effizienzgewinner
In der Gesamtbetrachtung bieten Faserlaser deutliche Energieeffizienzvorteile gegenüber alternativen Schneidtechnologien. Die Kombination aus hohem Wirkungsgrad, überlegener Schnittgeschwindigkeit und geringerem Nebenaggregat-Verbrauch führt zu Energieeinsparungen von 60-80% gegenüber Plasmaschnitten und 40-60% gegenüber CO₂-Lasern.
Die höheren Anschaffungskosten von Faserlaseranlagen amortisieren sich durch die Energieeinsparungen je nach Auslastung bereits nach 3-5 Jahren. Bei steigenden Energiepreisen und wachsendem Kostendruck erweist sich die Investition in energieeffiziente Lasertechnologie als zukunftssichere Entscheidung mit doppelter Dividende: für die Umwelt und die Wirtschaftlichkeit.
Wenn Sie weitere Fragen haben, zögern Sie bitte nicht, uns zu kontaktieren. Wir helfe Ihnen gerne weiter.
LGV CNC – Team
Schreibe einen Kommentar